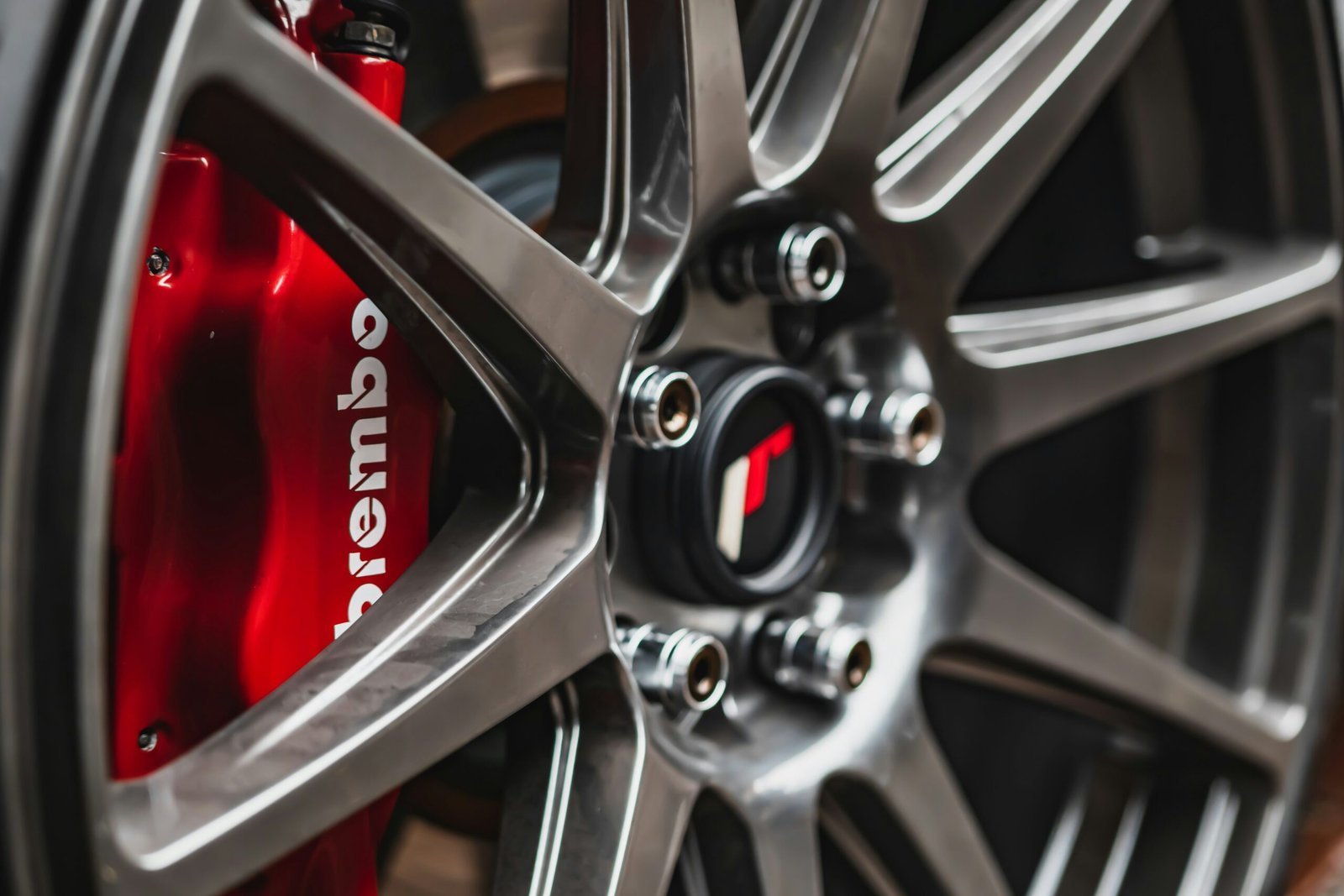
Overview of Junhe Aluminum’s Core Techniques
Junhe Aluminum, located in Ningbo, has established itself as a frontrunner in the aluminum manufacturing industry through the implementation of advanced core techniques. Central to their operations are three foundational processes: casting, extrusion, and alloying. Each of these techniques plays a vital role in producing high-quality aluminum products, catering to various industrial applications.
Casting is one of the earliest methods in aluminum processing, where molten aluminum is poured into molds to achieve desired shapes. At Junhe Aluminum, the casting techniques are refined to ensure minimal defects and optimal material properties. Utilizing state-of-the-art equipment, the company closely monitors temperature and composition, enabling precise control over the alloy properties. This focus on quality results in superior products that meet stringent industry standards.
Another crucial technique employed is extrusion, wherein aluminum billets are heated and forced through a die to create long shapes with consistent cross-sections. Junhe Aluminum has adopted innovations in their extrusion process, such as automated systems that enhance production speed while maintaining high dimensional accuracy. This process not only reduces waste but also allows for the manufacture of complex profiles that are in high demand across various sectors.
Alloying, the third technique, involves blending different metals with aluminum to enhance its mechanical properties, such as strength and corrosion resistance. Junhe Aluminum pays careful attention to the formulations used in alloying, which are tailored to specific applications and customer requirements. Their commitment to research and development enables them to explore new combinations of materials, thereby continuously improving their offerings.
The synergy of these core techniques has positioned Junhe Aluminum as a leader in the aluminum processing sector, as they strive to combine efficiency with precision. With a strong emphasis on quality assurance and innovative practices, the company remains dedicated to advancing the capabilities of aluminum production.
Advanced Machinery Utilized in Production
Junhe Aluminum stands at the forefront of the aluminum manufacturing sector, largely due to its investment in advanced machinery that enhances both efficiency and precision in the production process. Among the core equipment utilized are Computer Numerical Control (CNC) machines, which are pivotal in ensuring that each aluminum part is manufactured to exact specifications. These machines operate on pre-programmed sequences, allowing for unparalleled accuracy and repeatability, which reduces material waste and optimizes production time.
In addition to CNC technology, Junhe Aluminum employs induction furnaces for the melting of aluminum. Induction furnaces utilize electromagnetic induction to heat the metal rapidly and uniformly, facilitating a faster melting process compared to traditional methods. This technology not only improves energy efficiency but also contributes to the production of aluminum with superior quality, as it minimizes contamination risks during the melting stage.
Another critical component of the production line is the extrusion press, which shapes aluminum by forcing it through a die. This process allows for a diverse range of profiles and custom shapes, catering to various industry needs. The extrusion presses used at Junhe Aluminum are equipped with automation systems that ensure high throughput while maintaining consistent quality across batches. Each piece of equipment is regularly inspected and maintained, ensuring optimal performance and longevity.
The integration of cutting-edge automation technology throughout these machines significantly enhances the production speed, allowing Junhe Aluminum to meet the demands of a rapidly changing market. In summary, the advanced machinery at Junhe Aluminum exemplifies the company’s commitment to utilizing state-of-the-art technology, ensuring that high-quality aluminum parts are produced efficiently while adhering to stringent quality assurance standards.
Quality Control Processes at Junhe Aluminum
Quality control is a cornerstone of the manufacturing process at Junhe Aluminum, ensuring that every product meets the highest standards of performance and safety. To achieve this, Junhe employs a variety of rigorous testing methods designed to identify and rectify defects in aluminum components. Among these techniques, ultrasonic testing and X-ray inspection stand out as key processes that underscore the company’s commitment to quality assurance.
Ultrasonic testing utilizes high-frequency sound waves to detect internal voids and imperfections within aluminum parts. This non-destructive testing method allows for precise examination without compromising the material’s integrity. By sending sound waves through the aluminum, any inconsistencies can be identified while maintaining the structural properties of the components. This is especially critical for applications where reliability is paramount, such as in the automotive or aerospace industries.
X-ray inspection also plays a vital role in the quality control processes at Junhe Aluminum. This method allows for a detailed analysis of the internal structure of aluminum products, revealing defects that may not be visible through visual inspection alone. Utilizing advanced imaging technology, X-ray inspection ensures that any issues, such as cracks or voids, are detected early in the production process. This proactive approach not only enhances product quality but also reduces the risk of defects reaching the end user.
The emphasis on quality control at Junhe Aluminum is not solely about meeting technical specifications, but also about fulfilling customer expectations and compliance with regulatory standards. By integrating comprehensive quality assurance measures at every stage of manufacturing, Junhe reinforces its dedication to delivering high-quality aluminum products. This rigorous focus on quality control ultimately fosters customer satisfaction and builds trust in the Junhe brand.
Importance of Innovation in Aluminum Manufacturing
Innovation plays a crucial role in the aluminum manufacturing sector, influencing not only the techniques and machinery used but also the overall quality of the final products. At Junhe Aluminum, a commitment to continuous development exemplifies how advanced technological integration can significantly enhance production efficiency. The aluminum industry is characterized by constant demand for improvements, where the integration of cutting-edge machinery allows for precision and consistency in production processes.
Moreover, the adoption of innovative techniques in aluminum processing leads to substantial enhancements in product quality. With advancements such as automated systems and real-time monitoring, manufacturers can achieve tighter tolerances and reduce defects. This ultimately leads to greater customer satisfaction and higher market competitiveness. Junhe Aluminum’s investment in state-of-the-art machinery is a testament to its dedication to quality assurance and operational excellence.
Sustainability is another vital aspect that innovation addresses in the aluminum manufacturing sector. As global awareness of environmental issues grows, manufacturers are pressured to adopt eco-friendly practices. Innovative technologies, such as energy-efficient production methods and recycling processes, not only reduce the environmental footprint of aluminum manufacturing but also align with increasing regulatory requirements. Junhe Aluminum has recognized this trend and is committed to implementing sustainable practices alongside its advanced manufacturing techniques.
Looking towards the future, the aluminum manufacturing industry is expected to undergo further transformations driven by technological advancements. Trends such as Digital Twins, AI, and IoT integration are anticipated to reshape production methodologies significantly. Junhe Aluminum’s proactive approach to embracing these advancements ensures it remains at the forefront of industry developments, securing long-term success and competitiveness.
By prioritizing innovation, aluminum manufacturers can navigate challenges effectively while enhancing product quality, improving efficiency, and promoting sustainability—all essential components for thriving in a rapidly evolving market landscape.