Customized Services for Your Business
*Die Casting
Die castings are formed by injecting molten metal under high pressure into steel molds called “dies”. This process can provide a wide range of products because close tolerances can be consistently held and metal parts cab be produced efficiently and at high rates of production. The die casting process produces parts that are cost-efficient and highly engineered. The size of die castings can be as small as a matchstick and as large as 300 cubic inches. Tolerances in die casting can be held on the order of .003″ to .005″. Die castings are used in a wide variety of industries, including Agriculture, Mining, Construction Equipment, Commercial Machinery and Tools, Communications, Office Equipment, Military, Aerospace, Railroad, Automotive, Lighting and Medical.

Advantages
Die casting can produce both simple and intricate parts to near-net shape, reducing or eliminating the need for secondary operations such as machining and assembly. Although the tooling required for the die casting process has a relatively high initial cost, it has a long wear life. In high volume production runs, the cost per casting is lower than other casting processes. Minimal draft is required, compared to other casting processes. Casting surfaces are smoother than other casting processes. Holes and slots can be formed as part of the die casting without machining and hold very close tolerances. Parts such as studs, nuts, and bushings can be incorporated as composite integral parts of the die casting. These inserts can be made from aluminum, brass, steel, stainless steel, bronze and iron, and other materials.
*Parts Pattern Processing
The pattern shop is the first critical step in the production of castings. A high-quality casting can only result from a high-quality pattern. JUNHE Aluminum has operated an in-house pattern shop since its inception. The Company’s pattern makers have 30+ years of experience in pattern construction, molding, and machining. This experience facilitates the construction of basic and complex patterns from wood, metal, and resin from a single sample, drawing, or both. JUNHE Aluminum engineers also work with CAD or Solid Edge drawing files and interact with each customer step by step as required to assist them in meeting their casting requirements.
Requirements Comes First
JUNHE Aluminum meeting customer requirements comes first. The Company has a thorough process for reviewing and understanding Customer requirements. The Company also provides a full range of nondestructive testing to meet critical standards required by the end user. All of this understanding helps JUNHE Aluminum meet customer requirements.
When tooling is complete JUNHE Aluminum produces and evaluates samples to guarantee that the customer’s requirements have been met. Once sample approval is obtained from the customer, production is implemented. JUNHE Aluminum utilizes a disciplined system of process control to ensure that production castings meet customer requirements to ensure customer satisfaction.

*JUNHE Ensured Quality & QC uses to meet customer requirements include:
- Complete Casting Layout, inlcuding First Article Inspection.
- Calibration System.
- Provision of Physical and Chemical Properties.
- Wide Variety of Material Specifications.
- Heat Treatment under carefully controlled conditions in accordance with AMS 2771
- Complete Inspection of Castings.
- Fully trained, competent and qualified personnel for the performance and interpretation of Nondestructive Testing.
- Provision of the Results of Radiographic Testing up to a thickness of 5.5 inches
- Performance of, and Provision of the results of Fluorescent Penetrant Testing in accordance with MIL-STD-6866, ASTM-E-1417, MIL-STD-1907 and MIL-I-25135
- Provision of the results of Pressure Testing and Hydrostatic Testing up to 500 psi in accordance with customer requirements
- Comprehensive Sand Testing Capability on-site
- Casting Upgrade in accordance with customer requirements
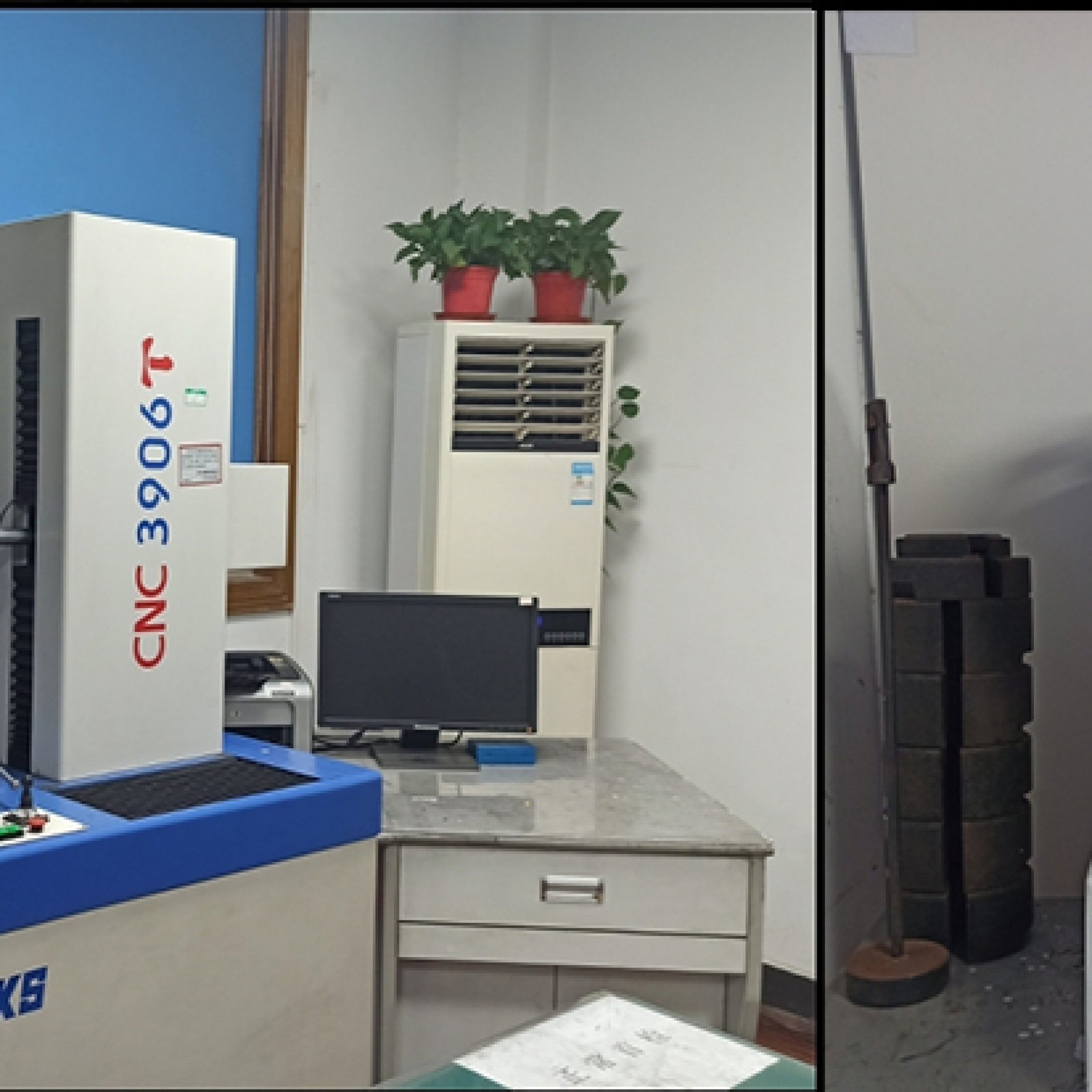



